Resources
-
Materials
Array -
- Anodizing
- Powder Coating
- CNC Machined
- Electroplating
- Painting
- Printing
- Laser Etching & Engraving
- EDM
- Drilling
- Tapping
- Heat Treating
- Annealing
- Quenching
- Aging
- Assembly
- Teflon Coating
- Impregnation
- Zinc Plating
- Chromate
- Brushed Satin Chrome
- Copper, Nickel and Tin Plating
- Alodine
- Cerakote
- E-Coating
Post Processes
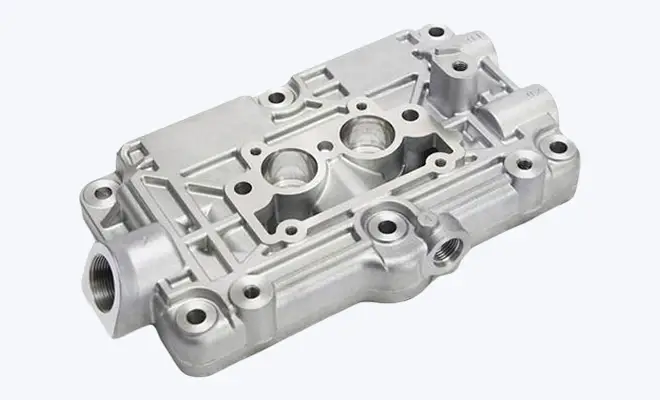
- Anodizing
- Powder Coating
- CNC Machined
- Electroplating
- Painting
- Printing
- Laser Etching & Engraving
- EDM
- Drilling
- Tapping
- Heat Treating
- Annealing
- Quenching
- Aging
- Assembly
- Teflon Coating
- Impregnation
- Zinc Plating
- Chromate
- Brushed Satin Chrome
- Copper, Nickel and Tin Plating
- Alodine
- Cerakote
- E-Coating
Technical Info
As the part length increases, the tolerance will also increase
Draft needs to be taken into account when designing for die casting with the minimum draft angle 2°
Minimum wall thickness for parts is 0.039”, but walls as thin as 0.020” can be die cast for smaller-sized parts
For lettering always use raised versus recessed, and use Sans Serif fonts that re equal to or r than 20 points and at least 0.020” thick
Avoid excessive changes in the cross section by designing gradual changes; uniformity is paramount for metal flow in the mold
Use ribs and blend them with external radii and fillets in an effort to remove sharp corners
In place of sharp corners and edges, design with a minimum radius of 0.015” – 0.031”
Ensure the parting line is as straight as possible
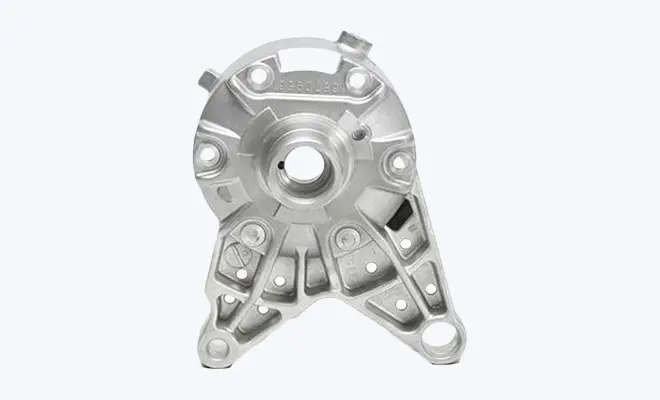
Materials
- Aluminum
- Magnesium
- Zinc
- Copper
Get in Touch with Us
Reach Out for Inquiries, Assistance, and More
Please contact us if you have any questions, comments or require
Need a Quote?
Features of our quoting system
Upload Files Directly
Just simply create an account, and upload your 3D files.
24 Hour Access
It can be hard to get things done over the phone, just use our system any time of day.
Digital Quotes
Upload your files, and we will send you a personalized quote.
Experienced Manufacturers
You can trust the brand Additive Manufacturing LLC
Best Prices
We offer competitive pricing to any client, small or large.
Register for your quote